With the development of science and technology, electronic, electrical and digital products are becoming increasingly mature and popular all over the world. Any component contained in the products covered in this field may involve soldering process, from large PCB board main parts to small crystal oscillator components. The vast majority of soldering needs to be completed below 300℃.Now the electronic industry chip level package (IC package) and board card level assembly are a large number of tin-base alloy filling metal welding, complete the device packaging and card assembly. For example, in the rewind chip process, the solder paste connects the chip directly to the substrate ;In electronic assembly manufacturing, solder paste is used to weld the components to the electrical subgrade board.
The soldering process includes wave soldering and reflow soldering, wave soldering is the use of molten tin circulating wave surface, and the PCB welding surface inserted with components in contact to complete the welding process; Reflow soldering involves placing solder paste or preformed pads between PCB pads and connecting the components to the PCB by melting the paste or preformed pads after heating.
Laser soldering is a soldering method in which laser is used as a heat source to melt tin to make the soldering parts close together. Compared with the traditional soldering process, this method has the advantages of fast heating speed, less heat input and less heat influence .Welding position can be precisely controlled; Welding process automation; Can accurately control the amount of solder, solder joint consistency is good; It can greatly reduce the influence of volatiles in the soldering process on operators, and it is non-contact welding, suitable for welding complex structural parts.
Laser soldering is based on the laser heat source as the main body, the tin filling melt solidification to achieve connection, conduction, reinforcement process effect. According to the state of tin material can be divided into three main forms: tin wire filling, tin paste filling, tin ball filling.
1. Application of laser welding tin wire in laser soldering:
Laser welding wire is a kind of main form of laser soldering, wire feeding mechanism with automatic workbench, automatically send tin wire through modular control mode and the light welding, has the characteristics of compact structure, one-time operation, compared to other soldering ways, its obvious advantage is one-time clamping materials, automatic welding, has wide applicability.
The main application fields are PCB circuit board, optical components, acoustic components, semiconductor refrigeration components and other electronic components soldering .Figure 1 is the product diagram of laser wire feed tin welding. It can be seen that the solder joint is full and has good wettability with the solder pad.
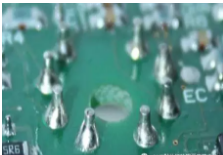
2. Application of laser solder paste in laser soldering:
Solder paste laser welding is generally used in parts reinforcement or pre-tin, such as the edge of the shielding cover through the solder paste in high temperature melting reinforcement, the magnetic head contact on the tin melting; It is also suitable for circuit conduction welding. The welding effect of flexible circuit board is very good, such as plastic antenna seat. Because there is no complex circuit, the solder paste welding often achieves good results. The solder paste filling welding can fully reflect its advantages for precision and micro - size workpieces. Because the solder paste heating uniformity is good, the equivalent diameter is relatively small, through the precision dispensing equipment can accurately control the amount of tiny point tin, solder paste is not easy to splash, to achieve a good welding effect .Due to the high concentration of laser energy, the uneven heat of the solder paste is easy to cause splashing, and the splashed tin beads are easy to cause short circuit, so the quality of the solder paste is very high, and the anti-splash solder paste can be used to avoid splashing. At present, the laser solder paste welding application has been very wide, successfully used in camera module, VCM voice coil motor, CCM, FPC, connectors, antennas, sensors, inductors, hard disk head, speakers, speakers, optical communication components, thermal sensitive components, photosensitive components and other precision electronic welding field.
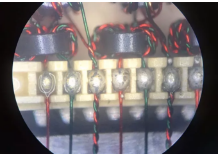
3. Application of laser tin ball in laser soldering:
Laser solder ball welding is a welding method in which the tin ball is placed in the mouth of the tin ball, heated and melted by the laser, and then it falls onto the solder pad and is wetted with the solder pad. Tin ball for no dispersion of pure tin small particles, laser heating melting will not cause splash, after solidification, full and smooth, there is no subsequent cleaning or surface treatment of the pads and other additional procedures. Good welding results can be achieved by using this welding method to solder fine pads and enameled wire

Difficulties in application of laser soldering technology:
Traditional soldering, wave soldering, reflow soldering, manual soldering iron soldering tin can solve the problem of soldering process of laser welding can be replaced gradually, but like SMT soldering (mainly for reflow soldering), the laser welding process is not applicable, because of some characteristics of the laser itself, also makes the laser soldering process is more complicated, specific summarized as:
1) For precision fine soldering, workpiece positioning and clamping is difficult, and welding sample and mass production are difficult;
2) Laser high energy density is easy to cause damage to the workpiece, especially for PCB soldering, substrate and metal lamination structure is not good, it is very easy to burn the plate, the sample defect rate is high and the cost is high so that customers can not accept;
3) The laser energy is highly concentrated, which is easy to cause the splash of solder paste, and it is easy to cause the short path in the solder welding of PCB board, leading to the scrap of the product;
4) For flexible wire, the consistency of clamping and positioning is not good, and the solder sample plumpness and appearance difference is large;
5) Precision soldering often has the requirements of wire feeding and tin filling, and it is difficult to automatically feed tin wire below 0.4mm wire diameter.
Laser soldering market demand profile:
Laser soldering at home and abroad have different degrees of development, although after years of development, there has been no big leap and application expansion, have to say that this is a weak spot in the application of welding .However, the market demand is constantly changing, there is not only the vertical number of growth, but also the horizontal application field is constantly expanding, with electronic and digital products related parts soldering process demand as the leading. It covers the soldering process requirements of other parts in various industries, including automotive electronics, optical components, acoustic components, semiconductor refrigeration devices, security products, LED lighting, precision connectors, disk storage components, etc. In terms of customer base, among them with apple customer product related parts derived soldering process requirements, including its upstream industry chain are looking for laser soldering process solution, overall, laser soldering in current and future for a long time there will be a spectacular explosion and a relatively large market size.
At the moment when the global economy is weak, Apple Inc. stands out. Its huge market share of digital electronic products and its huge global large-scale procurement drive the business growth of a large number of enterprises. The main products of these enterprises are electronic components, and tin soldering is an essential link in their production process. Enterprises, including suppliers of Apple Inc., are in urgent need of improvement and perfection due to the fact that the products produced are the latest and most high-end designs. They will encounter thorny technological problems in the process of mass production. Is a very typical field storage components industry, the head is a highly sophisticated and process requirement is very high storage components, head of the data line is commonly flexible PCB, were applied on the steel structure of body, the fine points of the array configuration need to advance on the end of tin, tin on the small quantity can only be done under a microscope, and the welding effect is extremely strict. Traditional way of welding is the manual welding, the welding operator level requirement is very high, the scarcity of labor resources and liquidity to produce huge uncertainty, moreover also impossible to quantify process standards (no process parameters, depend entirely on the human sensory judgment after welding effect), so need new welding process to overcome technical barriers. Laser soldering can quantify process parameters, improve yield, reduce costs, and ensure the standardization of production operations. With the increase of labor costs and the scarcity of skilled talents in the Chinese market, the manual demand for the traditional soldering field is slowly transformed into the demand for mechanized operation. Laser soldering will break through the traditional process and lead the trend .From the current customer welding sample, the popularity of laser soldering is the general trend.
Conclusion:
Because laser soldering has incomparable advantages over traditional soldering, it will be more widely used in the field of electronic interconnection and has a huge market potential.